变频器电路原理及检修方法
变频器在国内使用日益广泛和大量,变频器是相对高电压和大电流的设备,所以故障率也较高,维修量不少。网上对变频器维修的讨论不少,但从具体电子电路的分析入手来检修的不多。

图1是变频器的电路结构图。这是一个AC-DC-AC的变换过程。三相交流电(小功率的变频器使用单相交流)经整流桥整流后到滤波电容,得到直流电压。控制器控制六个大功率器件交替导通,电机线圈得到相对高频的交变脉冲电压,因为电机线圈电流不能突变,在线圈就会产生类似正弦波的三相交流电流,脉冲电压的频率是可控的,而电机的转速又跟频率成正比,所以变频器可以起到控制电机速度的作用。为了很好的控制使用变频器,在变频器加入了控制信号输入输出电路、电压电流检测电路、按键及显示电路、制动电路,当然也少不了电源系统给各功能电路提供电源。主电源由三相整流桥整流得到(小功率的变频器可见使用单相交流电源),整流后滤波电容充电的瞬间电流很大,对整流桥和电容的冲击会造成诸多问题。为了避免冲击,小功率变频器会在直流母线中串联热敏电阻,一般功率的变频器会使用继电器触点并接限流充电电阻的方式。此方式的原理是:变频器初始上电后,整流后电源通过限流电阻给后级滤波电容充电,串联的电阻限制了充电电流的大小,一个电压检测电路检测电容上的电压,当电压达到某个程度时,控制并联在限流电阻上的继电器触点闭合,此时整流后电源直接连充电电容,此时的电流就没有变频器刚刚上电时那么大了。电路既可以避免大电流冲击,又不致于让限流电阻长期串联在主电路中造成能量消耗和对后级的影响。在大功率变频器中,继电器则换成了可控硅,其原理也是一样的,只是可控硅比继电器机械触点能够耐受更大的电流。变频器停止输出后,机械负载因为惯性作用会带动电机继续转动,如果要设法使其迅速制动,电机线圈切割磁力线产生很高电压,电压经IGBT的C、E极上反并的续流二极管全波整流后加到直流母线,会使直流母线上的电压升高,这对电路元件会造成损害。能耗制动电路的原理就是通过检测直流母线上电压的大小判断电机是否处于制动状态,如果电压高到一定程度,电路控制制动IGBT导通,电容能量通过制动IGBT回路迅速消耗在制动电阻上,结果,电容上电压迅速下降,机械动能迅速转化为电阻热能,电机也就得以迅速停止转动。回馈制动的原理,在母线电压判断上与能耗制动相同,只是将能量回馈给了电网。
变频器主电源电路除了各元件的选择要匹配相应的功率之外,还要考虑电路缓冲问题。我们知道,高压大容量电容在充电初始阶段的充电电流是非常大的,如果不加限制,无论对变频器电路元件还是变频器输入电源的冲击都是相当大的,因此,变频器的电路设计上都有相应的对策。在微小功率的变频器而言,一般采用在充电回路上串联负温度系数热敏电阻(NTC)的办法,即常温下NTC的阻值较大,电路初始通电时可保证电容充电电流不会太大,一旦通电后NTC因发热阻值减小,此时电容的电压已经达到较高水平,因此充电电流既不会特别大,也不会影响电容向后级供电的需求。如图2所示,三相交流电压经桥式整流后串联RT5及RT6两个NTC给高压电容C133及C163充电。
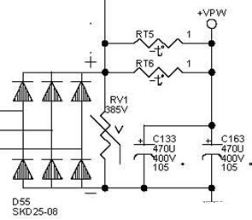
中小型功率的变频器的充电保护电路往往使用充电电阻和继电器的组合来实现缓冲保护。如图3所示,交流电源整流后通过串联的充电电阻R给电容充电,内部电路检测充电电压的大小,当电容电压上升至大于某个值时,继电器动作,触点K将充电电阻R短路,此时电流整流后直接给电容充电,因为电容上已经充电到一定电压,屏蔽充电电阻直接充电的电流冲击已经很小。电路的设计既避免了初始大电流的冲击,又避免了充电电阻对电路的持续影响。
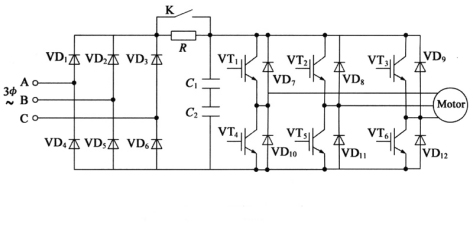
大功率的变频器,其主电源电路的缓冲电路,原理结构与中小功率变频器差不多,只是将继电器换成了可控硅,可控硅不存在继电器机械触点的冲击,可通过很大的电流,可靠性也得以提高。
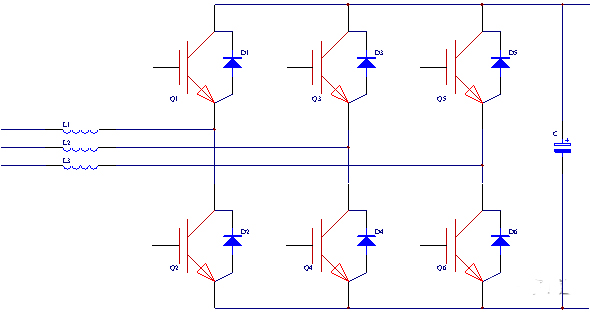
普通的变频器整流滤波电路,其直流母线上的电压,由于后级的负载变化而变得不稳定,电机制动减速作用产生的能量不能回馈电网,也导致直流母线电压的上升,对电路元件造成冲击。所以在高性能的变频器中,设计有可控的直流馈电电路。如图4所示,三相交流电源串联电抗器后通过并联在IGBT的C、E之间的二极管给电容充电,如果IGBT都不导通,这跟普通的桥式整流没有什么区别,而一旦IGBT有了合适的开关动作,电抗器回路被迫处于通断状态,其上产生的自感应电压就会叠加在电容上,因此,在电容上就可以得到比桥式整流更高的电压,可达600VDC以上。电容上的电压通过电子电路检测反馈到主控制板,主控制板精确控制6个IGBT的导通时序,既可以控制电抗器的电压正向叠加于电容,也可以控制电抗器电压在变频器制动减速时反向叠加于电容,此时电容上的电荷能量就回馈给电网,因此电容上的直流电压非常稳定。这电路有点类似于开关电源或者有源功率因数校正电路的Boost升压电路原理,通过电感和电子开关的配合来提升电容上的电压。
高压大电容容量下降、限流电阻开路、继电器触点损坏、继电器驱动电路异常、整流桥烧坏、制动IGBT异常、驱动模块异常,是变频器主电路常见的故障。高压大电容容量下降,会导致变频器启动后负载加大时主DC电压能量供应不上,电压跌落过大,变频器低压报警,而变频器制动时,电容容量不足又容易导致电容电压迅速上升,变频器过电压报警。限流电阻开路,则后端电容没有充电回路,变频器上电后主电容没有电压。如果小功率变频器控制板电源取自主电源,则控制电源都不会有电压,变频器通电就没有任何反应。如果继电器损坏,或者继电器线圈电流回路不上电,即变频器通电后继电器没有吸合(使用可控硅上电缓冲控制的变频器,可控硅没有被触发导通),则后级电路电流全部经过限流电阻,变频器启动后,电流增加,限流电阻分压增加,直流母线电压下降,会导致变频器低压报警。如果不报警,会因为限流电阻长时间通过大电流而烧断。所以,碰到限流电阻烧坏,维修不能仅仅只是换一个电阻,还要检查继电器的好坏及其控制电路的好坏。
变频器的开关电源和普通的AC-DC开关电源结构差不多,要能满足多路电压的需要,典型的变频器开关电源,包括主控制MPU电路电源(5V或3.3V)、主控制模拟电路电源(±12V或±15V)、I/O电路电源(24V)、驱动电路下桥臂驱动电源(15-20V)、驱动电路上桥臂3路独立驱动电源(15-20V),另外还可能设置一个DC-DC转换模块,提供通讯电路的独立电源(5V)。各路电源的取得,有些设计成一个开关变压器的多路独立副绕组整流滤波输出,有些设计成开关变压器副绕组只提供主控电路5V电源和I/O部分的24V电源,而驱动电路的电源再由24V部分经DC-DC变换得到。变频器开关电源维修方法参见前面部分的开关电源维修。
变频器的主控板电路可视为一个单片机系统,它包括了MPU、存储器、人机交互界面、I/O及通讯部分,还糅合了CPLD、DSP等大规模集成电路,内置软件算法,配合电压电流的适时检测信号,达到精准控制。对主控板电路的理解和检修可以完全按照单片机电路来对待。
变频器驱动控制电路是以驱动光耦为中心的,弱电控制强电的转换枢纽,在几乎所有的变频器设计中,此类电路几乎形成了固定的模式,即:控制6个IGBT,使用6个光耦,需要4组独立电源。下桥臂的3个IGBT因为发射极E连接在一起,3个光耦输出端电源就可以共用一组。
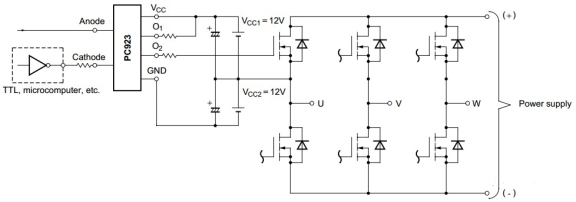
以IGBT专用的驱动光耦PC923为例,如图2.77所示,来自MPU的TTL电平信号控制PC923内部LED的发光,LED不点亮时,PC923输出O2是与GND导通的,功率管的门极G和源极S接近-12V的反偏置电压,功率管完全截止;PC923内部LED点亮时,O2和VCC导通,功率管的门极G和源极S接近+12V的正向电压,功率管导通。6个驱动光耦都是一样的结构。
变频器通电之前,应该先检测驱动模块是否大致正常。方法是,数字万用表选择二极管档,黑表笔接母线电压正极P,红表笔分别点测U、V、W输出,测试上端驱动桥电路,应该都显示导通0.5几伏正向管压降,如果显示短路,则相应的IGBT短路击穿,如果没有正向压降或者显示值过大,超过0.8V,则模块内部二极管损坏;然后红表笔接母线电压负极N,黑表笔分别点测U、V、W输出,应该都显示0.5几伏正向管压降,下端桥电路情况应该与上端情况一样。在变频器上电之前还应该测试驱动电路是否每一路都有效可控,以免上电就炸功率模块或者驱动不良。测试的方法是,不要加母线电压,只加控制电压,就是想办法不让驱动模块的PN之间有高电压。给开关电源上电后,检查驱动光耦电源是否正常,然后使用指针表x10Ω档依次在光耦输入端注入电流,同时使用数字表二极管档检测对应的IGBT是否导通,如果每一个IGBT都可以控制导通和截止,且当IGBT截止时G、E之间是负电压,且当IGBT导通时G、E之间是正电压,说明驱动电路大致没有问题。为了确保驱动电路和IGBT完全没有问题,还要做进一步的检测,因为虽然以上检测方法可以确认驱动电路能够有效动作,但是高速脉冲驱动的情况并没有被模拟到,如果某些驱动部分元件的特性变差,变频器高速运行时可能出现问题,另外因为此时模块还没有加高电压,高电压下模块的表现如何也未知。进一步测试,可以将数字电桥置于电容测试档,10khz,1V输出电压,D值,在线测试上桥三路IGBT的G、E之间电容,然后测试下桥三路IGBT的G、E之间的电容,电桥显示的电容量和D值,上桥三路应该一致,下桥三路也应该一致,如果哪一路电容量或D值和其它两路差别较大,就判断这一路存在问题,然后从这一路入手检测,找出对应的原因。最后对各IGBT进行耐压测试,保证IGBT的耐压符合数据手册的规定。
变频器的直流母线电压是重要的检测对象,检测分为比较检测和定量检测两类。比较检测是将检测到的电压和设定电压相比较,判断电压到位、过高或过低,及时输出控制信号,要求反应速度快;定量检测将检测到的电压进行数字量化,提供给主控板做数据处理。
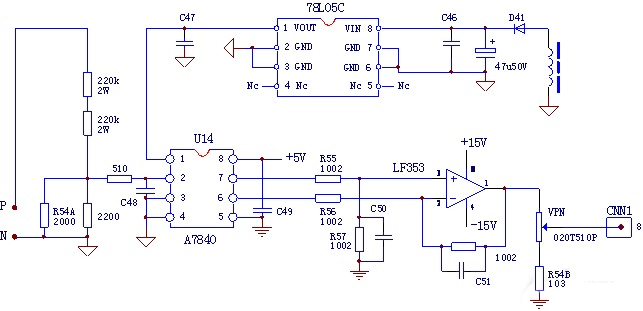
图6所示是一款变频器电压检测电路。直流母线电压经过两个220KΩ降压电阻,在另两个2kΩ和2.2kΩ并联的电阻上得到一个随母线电压成正比变化的mV级电压,这个电压加到隔离放大器A7840的输入脚第2、3脚之间,经过8倍的幅度放大,在6、7脚输出。运算放大器LF353和周边元件组成差动放大器,输出电压大小是U14的6、7脚的电压差值,虽然电压幅度没有放大,但电流驱动能力提高,输出电压经电位器取样调节到合适的幅度再送后级电路处理。A7840的输入端电源和输出端电源是隔离的,输入端电源是由开关变压器的一组副绕组经整流、滤波及78LC05稳压后得到。输出端电源则是和主控板共用的。
电压检测电路容易损坏的是隔离放大器如A7800、A7840之类的芯片,这类芯片可以在线检测,方法是:控制电源通电后,万用表mV档分别测试输入电压即2脚对3脚之间的电压,然后再测试输出电压即6脚对7脚之间的电压,输出电压应该是输入电压的8倍,如果相差较大,则隔离放大器芯片损坏。另外一个比较有效的判断方法,就是当2,3脚输入电压是0mV,输出电压7脚对6脚电压低于-20mV(例如-23mV),则判断隔离放大器损坏。另外有些电压检测电路是非隔离的,但是电压采样电路的结构是一样的,经常容易损坏的是接正极P端的取样电阻,此电阻开路或阻值变大会引起低电压报警。
小功率变频器的电流检测电路是采用在输出回路串联mΩ大小的采样电阻,在电阻上产生mV级的电压降,这个电压既不会给输出回路带来影响,又能符合隔离放大的输入范围。大功率变频器的电流检测则是采用霍尔传感器,利用输出导线穿过传感器产生的磁场大小来测定电流大小,霍尔传感器输出一个跟电流成正比的电压或电流信号,信号再送后级电路处理。
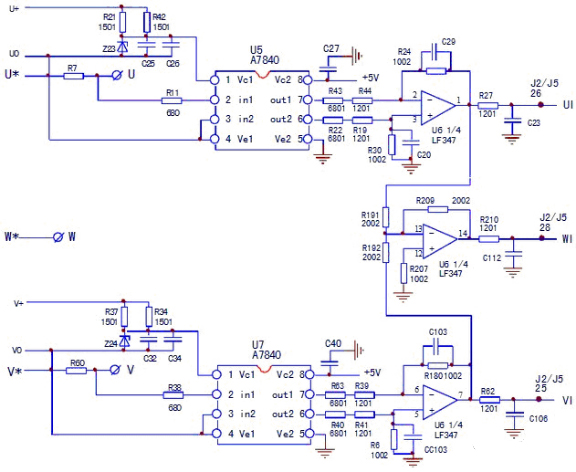
图7是串联电阻方式的变频器电流检测电路,在U相和V相分别串联了采样电阻R7 、R60,W相没有串联采样电阻,但是知道U、V相电流后可以计算得到。当采样电阻有电流流过时,产生的电压降加到A7840的2、3脚,经过隔离放大8倍后从6、7脚输出。这些电流是有方向性的,A7840的6、7脚输出电压差值可能是正的,也可能是负的,但U、V、W三相电流的代数和为0,根据这一规律,已知U、V相电流大小方向,就可以采用运算放大器的加减法电路来设计得到W相电流的大小方向。图8是常见霍尔电流检测器及接线方法,检测器使用双电源,M脚是电流输入输出脚,M脚和0V端接有取样电阻RM,通过RM的电流方向和大小可以反映穿过霍尔电流检测器的电流方向和大小,即可在M端取得反映大电流的方向和大小的电压。
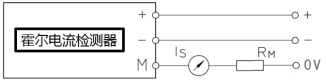
变频器电流检测电路损坏会导致电路过流报警。有时候电机转动时会有异响却并不报警,这往往是电流检测电路的问题,因为检测到的某一相电流与实际电流并不一致,导致变频器输出力矩失算,造成三相不平衡,从而挤压电机轴承,发出异常声音。
对于使用隔离放大器检测电流的电路,维修检测方法和上面介绍的使用隔离放大器检测电压的电路差不多。对于使用霍尔电流检测器的电流检测电路,维修注意重点检测霍尔检测器是否失效。可以在变频器没有运行,0电流时检测器信号输出电压应该也是0V,如果和0V偏离太大,1V以上,则电流检测器损坏。也可以使用导线在霍尔检测器穿心孔绕多几圈,导线通电后,对比检测两个霍尔电流检测器输出电压大小,不应该出现明显差异。
变频器驱动电路维修的常见故障原因分析